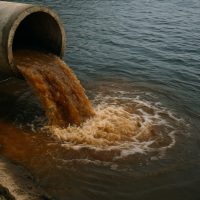
A group of academics with expertise in economics, water governance and legislation, in an exclusive report seen by The Guardian, found that public ownership of the water industry is the best way to...
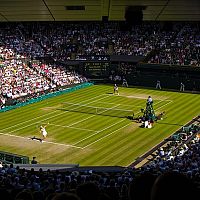
Campaigner group Save Wimbledon Park (SWP) is calling for public backing of their plan to challenge the planning permission for the expansion of Wimbledon tennis courts by the All England Lawn Tenn...
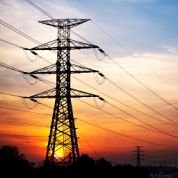
An energy storage system proposed to be built on grey belt land in Lancashire has been approved following an appeal.
"Grey belt" land is a relatively new concept. It is considered in nation...
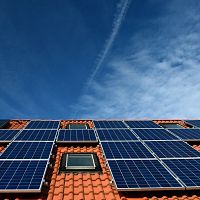
According to the latest Public Attitudes Tracker from the Department for Energy, Security and Net Zero (DESNZ), public support for renewable energy in the UK has dropped.
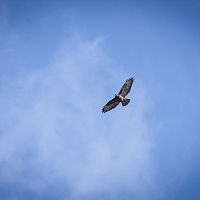
Researchers have found that 500 bird species could vanish within the next century, calling for urgent "special recovery programmes" such as captive breeding and habitat restoration to rescue unique...
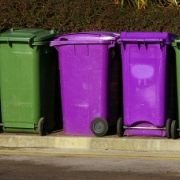
Following a consultation that ran from 11 November 2024 to 20 January 2025, the Environment Agency has introduced new charges aimed at tackling waste...
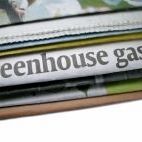
The European Commission has announced that the EU should cut its emissions by 90% by 2040, in a proposed change to its climate law that falls short of what its scientists ha...
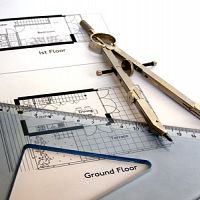
The Planning and Infrastructure Bill has passed its second reading in the House of Lords after several hours of debate.
Second reading is the first opportunity for m...
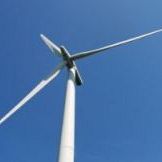
Net Zero Week starts tomorrow (Saturday 5 July), which is the UK's official national awareness week and the biggest net zero conference.
It brings together all the stakeholders needed to re...
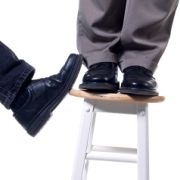
Work-related fatalities fall slightly but remain a serious concern, the Health and Safety Executive (HSE) has reported.
The HSE has published...
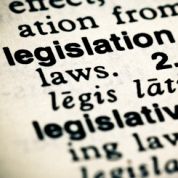
The government has published the Employment Rights Bill Implementation Roadmap, which sets out ti...
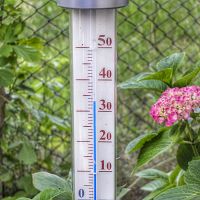
It is a question that pops up every summer and has started to appear in the recent UK heatwaves: when is it too hot to work? As these summer heatwaves increase, employers need to consider the effec...
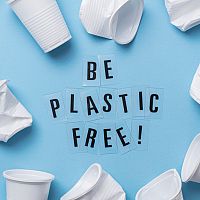
July is plastic free month - a global movement to reduce single-use plastic and protect our planet!
Why it matters
Globally, we produce over 400 million tonnes of p...
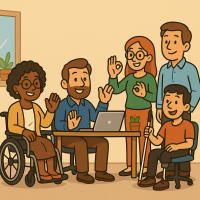
Disability Pride Month starts today (1 July), which is an important moment for disabled people to come together as a community.
It is an opportunity to share experiences and start conversat...
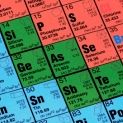
The Health and Safety Executive (HSE) has unveiled a wide-reaching programme of reforms to modernise Great Britain’s chemicals regulatory framewo...